With the development of the craft beer industry, OSHA violations have also increased. According to the US Bureau of Labor Statistics, between 2010 and 2015, the number of OSHA violations by craft breweries more than doubled. Now, the craft beer industry is paying more and more attention to employees and will strictly abide by OSHA requirements.
Craft breweries usually employ professional brewers, who need to handle hazardous chemicals and hazardous equipment in confined spaces. Many beer brewers will open to the public to visit and taste, which makes the brewers face further responsibilities. Craft breweries must follow OSHA requirements for breweries to ensure the safety of employees and customers. Micet Craft will provide you with some ideas on best safety practices by providing an overview of OSHA regulations, violations, and compliance, and help you make the brewery safer and more reliable.
7 common OSHA violations in the beer brewing industry
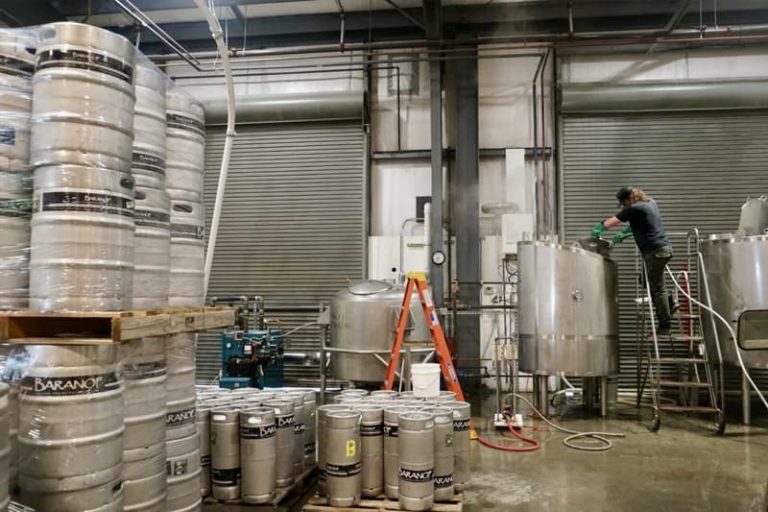
Access to confined spaces requiring permission
Brewing beer requires employees to clean and repair fermentation tanks, silos, kettles, and other equipment, as well as processing wort. According to OSHA regulations, if these spaces are relatively small, they can be regarded as confined spaces. Craft breweries need to assess whether the space meets the PRCS standards. If PRCS is recognized, the brewery must post a warning to employees.
If employees must enter a Permitted Confined Space (PRCS) for work, the brewery is obliged to maintain a space plan that requires written permission. This plan needs to include more staff training, monitoring the atmospheric conditions of the space, and formulating emergency rescue plans.
OSHA defines a «confined space» as an area that meets the following three conditions:
- It is large enough and well configured so that the employee’s body can enter and perform the assigned work;
- It has limited or restricted means of entering or exiting space;
- It is not designed for employees to work continuously;
How to avoid this violation
OSHA requires many safeguards to ensure safety in confined spaces that may cause harm to workers, including:
- OSHA requires a written plan to identify and test possible hazards. It also needs to test the atmospheric conditions of the confined space and develop emergency rescue plan instructions;
- The brewery must correctly identify the PRCS as a potential hazard by posting a warning;
- Employees must get an entry permit signed by the entry supervisor before they can enter the confined space to work;
- The person in charge of the brewery must provide necessary training and guidance for employees who may work in confined spaces;
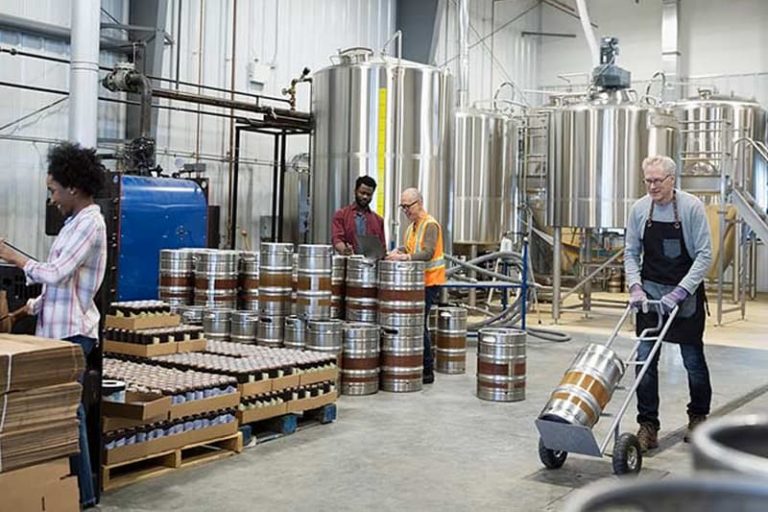
General Liability Clause
According to the general liability clause, OSHA requires breweries to provide employees with a workplace that «has no recognized hazard that causes or may cause death or serious bodily injury.» This includes ergonomic hazards. Working in a craft brewery usually requires moving heavy kegs or lifting bags of malt grain. So, breweries that fail to mitigate or move heavy objects or improper handling are often cited under the general liability clause.
How to avoid this violation
- Employees must receive relevant job training before starting work, and they need to be reminded of the correct work skills frequently;
- Provide employees with appropriate tools and equipment (for example, forklifts) to lift heavy objects, and ensure that employees receive appropriate training and can use them correctly;
- If possible, consider setting up a work schedule to allow many employees to share the responsibilities of handling. For example, many workers can be used to carry grain;
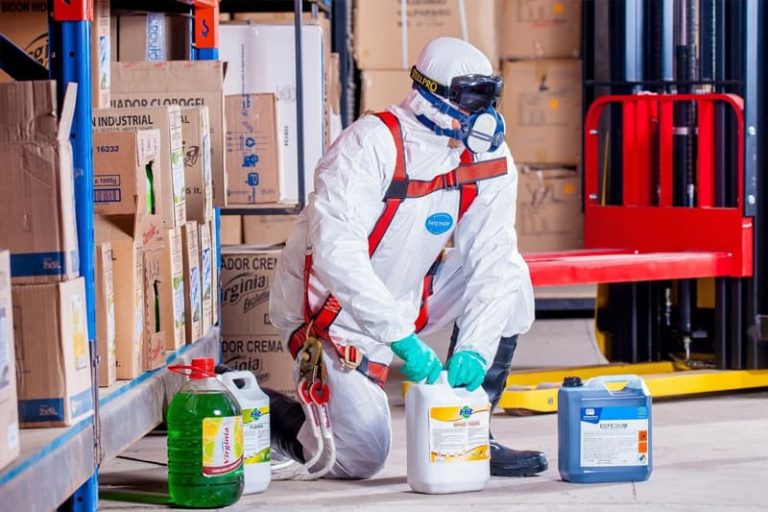
Safety Management of Hazardous Chemicals
To help ensure a safe and healthy workplace, OSHA has issued the High-Hazard Chemical Process Safety Management (PSM) standard, which contains requirements for managing the hazards associated with processes that use high-risk chemicals. Companies not only need to follow PSM standards, but they also need to keep proper paperwork about the use and handling of any hazardous chemicals.
Brewers also use hazardous chemicals (especially concentrated ones) for cleaning, sanitation, and other purposes in the brewery. Common chemicals include acids (low pH), alkalis (high pH), and flammable chemicals. Alkaline or alkaline chemicals are commonly used to clean brewery equipment, storage tanks, and packaging materials, such as sodium hydroxide, sodium hypochlorite, and potassium hydroxide. Brewers also use acids with similar effects, such as phosphoric acid, hydrochloric acid, nitric acid, and iodine-based chemicals. Alkaline chemicals and acids are corrosive to human tissues and are especially dangerous to the eyes. Appropriate personal protective equipment is important to ensure a safe working environment, such as entering tanks for maintenance work.
In the beer brewing process, some complex chemical reactions are involved. Also to the chemicals mentioned above, carbon dioxide, oxygen, and ammonia are also used in the brewing process, from oxygenating the wort to cooling equipment. The brewery needs to check some key gases, and ammonia is one of them. Ammonia is an efficient coolant, especially suitable for use as a refrigerator in food and beverage processing, so breweries also rely on these chemicals to maintain low temperatures. Ammonia is also a hazardous chemical, so it is subject to OSHA’s PSM rules.
How to avoid this violation
- Conduct process hazard analysis: According to OSHA, process hazard analysis is a thorough, orderly, and systematic method that can be used to identify, test, and control the hazards of highly hazardous chemicals in the design;
- Develop written procedures; develop written procedures for the safe operation and maintenance of the refrigeration system. Especially in the case of ammonia leakage, do not use the unique smell of chemical substances as enough early warning signal;
- The fixed gas detection device can accurately measure the ammonia concentration in a specific location and quickly remind workers of changes in air quality. The fixed gas detection device can also be used in conjunction with an automatic controller to program the fixed gas detection system to automatically shut down the operation when the air quality reaches a dangerous level;
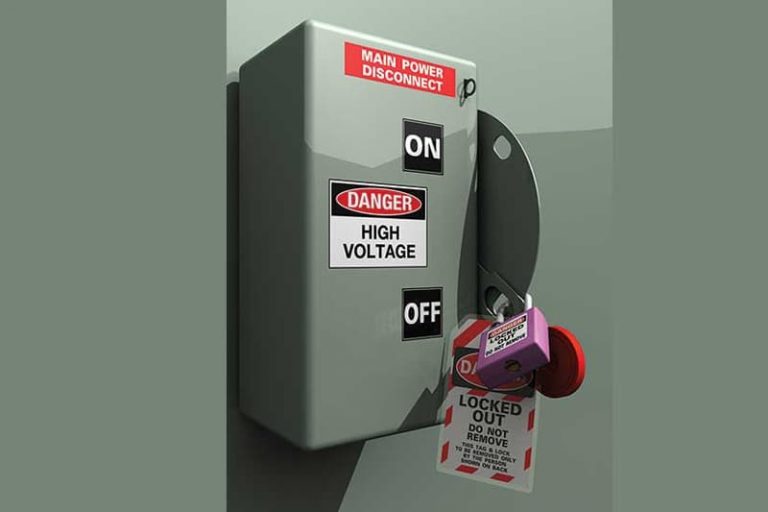
Control of hazardous energy (lockout/Tagout)
A large number of large machines are needed to work together in a brewery. When employees are responsible for the maintenance and upkeep of brewery equipment, accidental start-up of machinery or accidental release of storage capacity may pose serious risks. Employees must be trained on how to prevent accidental activation and accidental release of storage capabilities, which are part of OSHA’s LOTO guidelines.
Staff training is an important part of the comprehensive energy control plan for all breweries. The LOTO plan must also include the use of authorized energy control equipment to lock or tag equipment so that employees can easily verify whether energy has been effectively isolated.
How to avoid this violation
- Develop and implement LOTO or energy control plans. As part of the plan, before performing service or maintenance, choose a worker to shut down the machine or equipment and disconnect it from its energy source;
- Authorized LOTO equipment should be used to lock or mark the equipment to verify that the energy has been effectively isolated and prevent the release of hazardous energy;
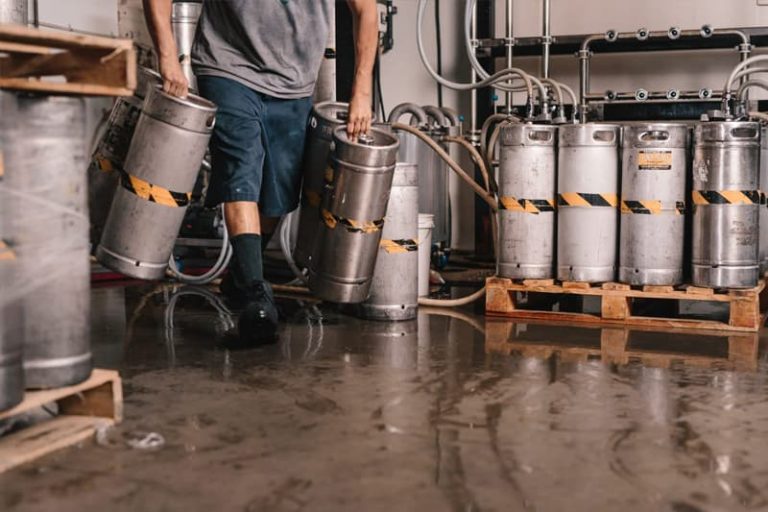
Dangerous communication
Hazard communication guidelines ensure that employees understand any hazardous substances or the environment. Also to the ammonia used for refrigeration in the brewery, various other chemicals, such as detergents and disinfectants, need to be used. To ensure the safety of chemicals, information on the characteristics and hazards of all chemicals should be accessible and understandable. This includes marking chemicals and identifying storage spaces for hazardous chemicals to make chemical safety information easy to get. Breweries should incorporate these practices into their hazard notification plans and train workers on how to properly check the presence of chemicals.
How to avoid this violation
- The brewery should develop a hazard communication plan;
- Chemicals should have complete labels and attached safety data sheets;
- Train employees how to properly handle and check the presence of chemicals;
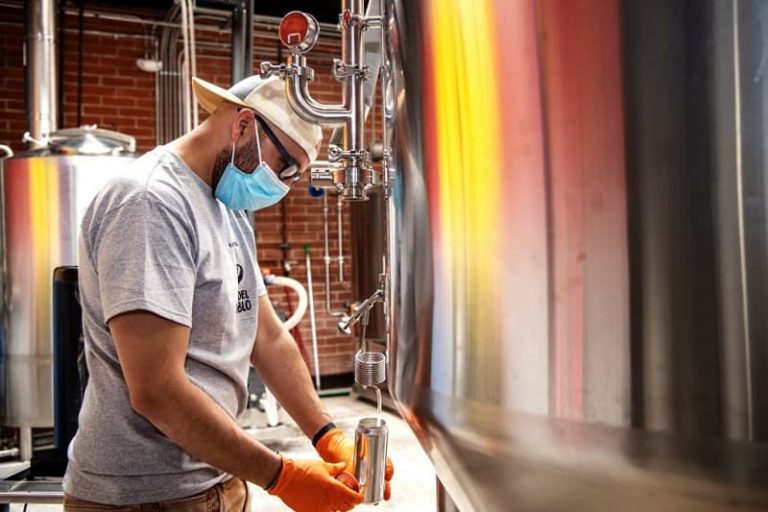
Eye and face protection
Useful craft breweries are usually small businesses, so it is easy to overlook appropriate personal protective equipment (PPE), especially face and eye protection. According to OSHA regulations, companies must provide the correct PPE to protect their employees, especially when dealing with hazardous work such as boiling water or toxic chemicals. In craft breweries, appropriate personal protective equipment may include work clothes, gloves, goggles, or full-face masks.
How to avoid this violation
To follow OSHA standards, breweries should provide workers with appropriate eye and face protection;
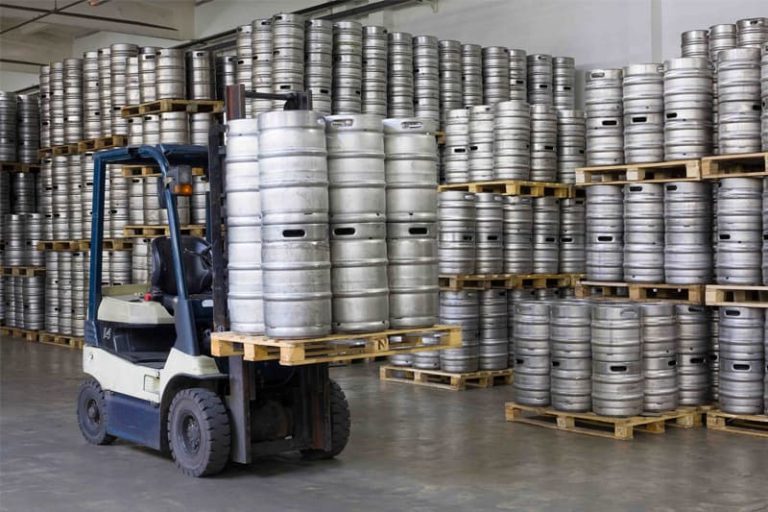
Powered Industrial Truck Danger
Craft breweries often rely on powered industrial trucks and forklifts to transport and lift heavy objects and raw materials. Despite this, many breweries are still cited for failing to train employees to operate such equipment safely.
How to avoid this violation
OSHA requires brewery managers to train their employees to drive and operate forklifts and power trucks. The training content is as follows:
- Trainees can only operate forklifts and electric trucks under the supervision of colleagues or managers who have training knowledge and professional knowledge;
- Training must be conducted in a way that does not endanger the personal safety of employees;
- Training must include formal teaching, practical training, and assessment of the abilities of the trainees;
- Training should cover many topics related to the safe operation of electric trucks and forklifts, such as steering, how to use controls and instruments, etc;
Although the craft beer business is known for its fashion and fun, skilled operation of any size brewery requires a high degree of process knowledge, training reserves, and skill. As the craft brewing industry develops and becomes more and more mainstream, it will become very important for brewers to educate themselves and their employees on proper safety practices. In this way, the brewery can not only avoid OSHA violations but also protect the brewery employees from harm.
Get the price of brewery equipment
The craft brewing industry is developing rapidly, and more and more people want to open a craft brewery. If you want to get a competitive price for brewery equipment, you can contact Micet Craft directly. Our engineers will provide you with the list and prices of the equipment needed to start the brewery. Also, Micet Craft will also provide customers with customized turnkey solutions. If you are about to open the brewery, please contact us, Micet Craft very much hopes to cooperate with you!