Table of Contents
What is a mixing tank?
The mixing tank is an industrial equipment used for mixing, emulsifying, and mixing different materials. It is widely used in industries such as chemical, pharmaceutical, food, and bioengineering for process operations such as mixing reactions, heating, or cooling. The mixing tank can be equipped with heating, cooling jackets, and temperature control systems to meet different process requirements.
Features of the mixing tank:
- Good sealing performance: The mixing tank is usually equipped with a sealing device to prevent the leakage of the mixing material and maintain the pressure or vacuum environment in the tank, which is suitable for some industries that require an aseptic operation.
- Controllable temperature and pressure: The mixing tank can be designed with a structure with a heating or cooling jacket, and the temperature of the material in the tank is adjusted by controlling the substance in the jacket. Some mixing tanks can also withstand a certain pressure and are used in some special chemical reaction processes.
- High mixing efficiency: The mixing tank can accelerate the uniform mixing of materials and increase the reaction speed through the rotation of the agitator, which is suitable for processing large-capacity materials.
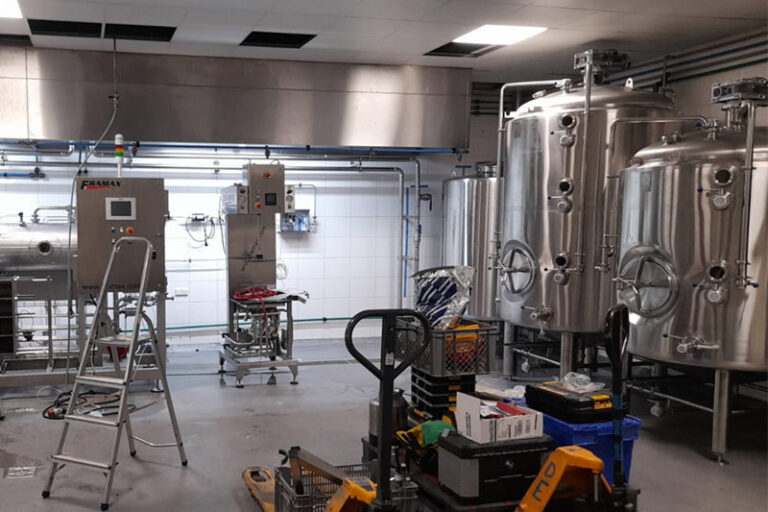
Materials of Mixing Tanks
- Carbon steel: Carbon steel mixing tanks have high strength and pressure resistance, are suitable for materials with low corrosive requirements, and have relatively low cost. They are often used in general aqueous solutions and environments without corrosive gases.
- Stainless steel: Stainless steel mixing tanks are widely used on occasions with high corrosion resistance requirements, especially in food, medicine, chemical, and other industries. 304 stainless steel is suitable for materials at room temperature and with low corrosiveness, while 316 and 316L stainless steel perform better in high temperature and strong corrosive environments.
- FRP: FRP mixing tanks have excellent corrosion resistance, especially for some high-concentration acid, alkali, and salt solutions and organic solvent environments. In addition, FRP is light in weight and high in strength and is often used in large equipment, but its temperature resistance is not as good as that of metal materials.
The main components of the mixing tank
- Tank body: The main container of the mixing tank, usually made of stainless steel or other corrosion-resistant materials, is used to hold materials. The tank body can be designed into different volumes and shapes according to needs.
- Agitator: Used to stir the materials in the tank. Common types of agitators include paddle, spiral, anchor, turbine, etc. The choice of agitator depends on the characteristics of the material and the purpose of stirring.
- Drive device: Generally composed of an electric motor and a reducer, the agitator is driven to rotate through a power transmission system. The power, speed, and structure of the drive device will be designed according to the working requirements of the mixing tank.
- Shaft sealing device: Installed at the outlet of the agitator shaft to prevent leakage of materials in the tank. Commonly used shaft sealing devices include mechanical seals and packing seals.
- Heating or cooling device: Sometimes it is necessary to heat or cool the materials in the tank, which is usually achieved using a jacket or built-in heat exchanger. The jacket is located on the outer layer of the tank body and is used to pass heating or cooling materials.
- Temperature, pressure, liquid level, and other measuring devices: Used to monitor the temperature, pressure, and liquid level in the tank in real-time to ensure that the mixing process meets the process requirements.
- Bracket and base: Support the entire mixing tank and install it firmly in the workplace.
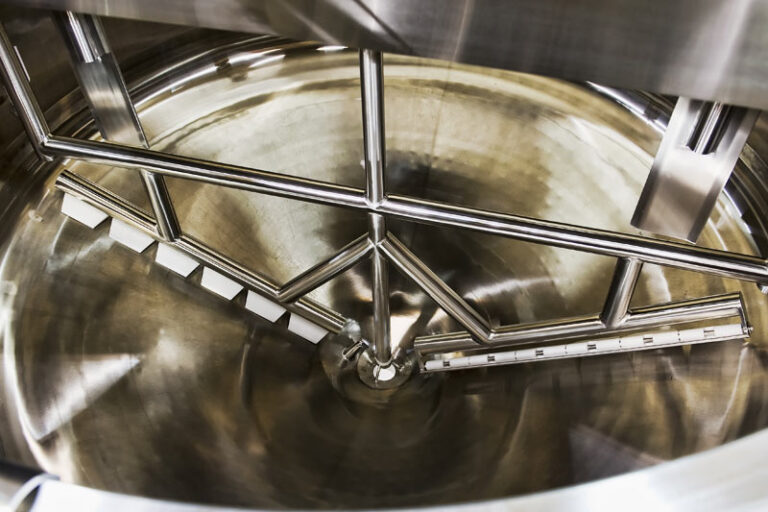
Types of Agitators
- Paddle Agitators: Paddle agitators are one of the simplest agitators and are shaped like a boat paddle. They are often used for stirring and mixing low-viscosity fluids. There are many types of paddle agitators, such as flat paddles, inclined paddles, and curved paddles.
- Anchor Agitators: Anchor agitators are shaped like an anchors and are used for mixing high-viscosity fluids. The blades usually rotate close to the tank wall, which helps to scrape off the adhesion of the tank wall and enhance the heat transfer effect. They are suitable for stirring viscous liquids or those with sediments.
- Ribbon Agitators: The blades of ribbon agitators are in the shape of a spiral ribbon and are usually used for stirring high-viscosity, non-Newtonian fluids, such as cosmetics, coatings, and food processing. It can effectively promote the up and down flow of fluids and increase the uniformity of stirring.
- Propeller Agitators: Propeller agitators are similar to marine propellers and are suitable for rapid mixing of low-viscosity liquids. It produces axial flow and can be used in large-volume mixing tanks that require high-speed stirring.
- Turbine Agitators: Turbine agitators have short and flat blades, similar to discs, and can be divided into open and closed types. It produces strong radial flow and is suitable for mixing occasions that require dispersion, such as solid-liquid and liquid-liquid.
- Frame agitator: The frame agitator has a structure similar to a frame and is mostly used for high-viscosity liquids and mixing processes that require uniform heat transfer. The frame is close to the tank wall and can better scrape off the attachments on the tank wall.
- Double-helix agitator: Double-helix agitators are usually used for fluids with solid particles or high-viscosity materials. They are suitable for materials with special rheological properties and can form a good circulation flow in the tank.
How does the mixing tank participate in brewing?
- Material addition: First, the raw materials or liquid materials are added to the mixing tank. These materials may be a single substance or a mixture of multiple substances, depending on the needs of the production process.
- Heating or cooling: If the production process requires, the inside of the mixing tank may need to be heated or cooled. This is usually achieved through the external jacket of the tank, a built-in heater, or a cooling system.
- Stirring and mixing: The materials are added and the stirring device starts to operate. The purpose of stirring is to mix the different ingredients evenly and ensure the uniformity and stability of the materials.
- Chemical reaction: For some applications, the mixing tank is not only used for material mixing but may also involve chemical reactions. For example, a chemical reaction mixing tank needs to ensure that the reactants are evenly mixed to promote the reaction.
- Detection and control: During the stirring process, sensors and instruments are used to monitor and detect parameters such as temperature, pressure, stirring speed, and material concentration. Adjust these parameters as needed to maintain the stability of the production process.
- Discharging: After the stirring and reaction process is completed, the material will be discharged through the discharge port. Some mixing tanks may also be equipped with filters, centrifugal separators, and other equipment for further processing of materials.
- Cleaning and maintenance: After each batch, the mixing tank needs to be cleaned to avoid cross-contamination or material residue. This usually requires high-pressure cleaning, sterilization, etc.
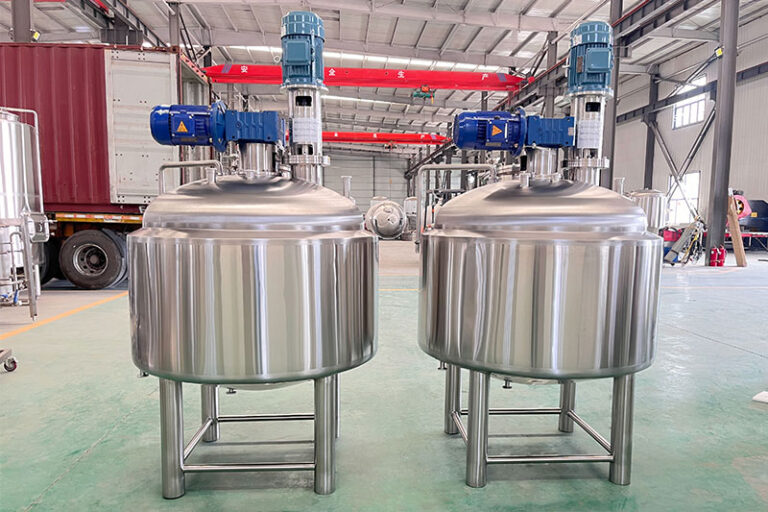
FAQ
How to choose a suitable agitator?
The selection of an agitator should take into account the brewing process and the need for agitation. The main factors include the type of agitator, speed, corrosion resistance, material, and mixing uniformity. The agitator should be able to effectively mix the wort or yeast, avoid excessive oxidation or bubble generation, and ensure long-term stable operation.
What is the corrosion resistance of a stainless steel mixing tank?
Stainless steel mixing tanks usually have strong corrosion resistance, but the specific performance depends on the material used. 316 stainless steel has better corrosion resistance, especially for strong acid and alkali environments. However, if it is exposed to chemicals for a long time, corrosion may occur.
What is the reason for the agitator to stop suddenly during operation?
The sudden stop of the agitator may be caused by the activation of the motor overheat protection, power supply problems, or equipment failure. Check the working status of the motor, and the power connection, and whether the various parts of the equipment are operating normally.