What is a stainless steel brewing tank?
Stainless steel brewing tanks are containers specially designed to hold and handle beer at various stages of brewing. These tanks are highly regarded for their durability, corrosion resistance, and ability to maintain precise temperature control. They are available in a variety of sizes, designs, and customizations to suit home brewers, craft breweries, and large enterprises.
These tanks are made of food-grade stainless steel, usually 304 or 316 grades, to ensure that the beer is not contaminated. They are indispensable in modern brewing because they can withstand high pressure and maintain a sterile environment.
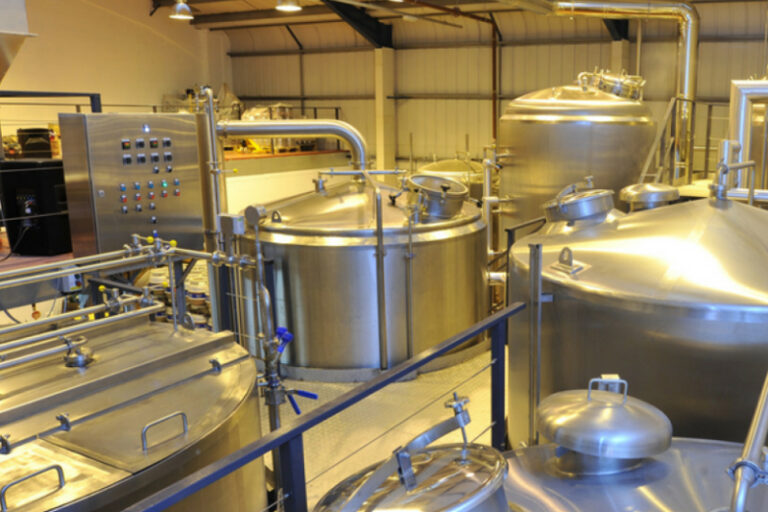
Brewing process in a brewery
- Malt Preparation: One of the main raw materials for beer is malt. First, the malt is crushed and ground into malt powder. This process separates the outer shell of the malt from the internal sugar, preparing for the subsequent mash
- Mashing: The mashprocess is to mix the malt powder with hot water and heat it to a specific temperature to convert the starch in the malt into fermentable sugar.
- Filtration: After mash, the liquid part is separated from the solid residue (malt residue), a process called filtration. After filtration, the sugar liquid will enter the washing stage, and the residual sugar will be further extracted by spraying hot water.
- Boiling: The filtered wort will be sent to the boiling pot and boiled at high temperature. This stage has two main functions: boiling can eliminate the miscellaneous bacteria in the wort and ensure the hygiene of the beer. During the boiling process, hops are added, which can give the beer a unique bitterness, aroma, and some antiseptic effect.
- Cooling: The temperature of the wort after boiling is very high, so it needs to be quickly cooled to a temperature suitable for fermentation (usually 18-24°C, depending on the type of beer). Rapid cooling can prevent bacterial growth and ensure smooth fermentation.
- Fermentation: The cooled wort will be transferred to the fermentation tank and yeast will be added. Yeast converts the sugar in the wort into alcohol and carbon dioxide, producing alcohol and bubbles during the fermentation process.
- Maturation: After fermentation is completed, the beer enters the bright tank tank. This stage usually lasts for several days to several weeks. The purpose is to make the beer taste more mellow, impurities settle, and the beer becomes clearer.
- Packaging: After sufficient maturity and clarification, the beer is ready to enter the packaging stage. At this time, the beer can be bottled, canned, or kegged and is ready for sale.
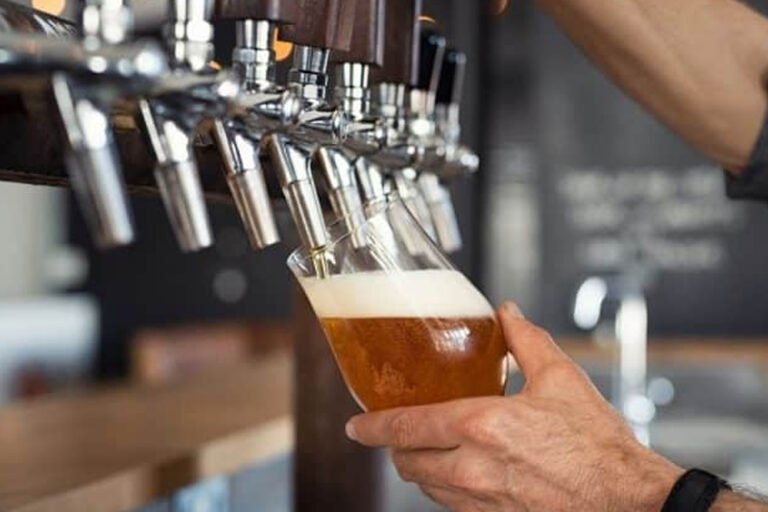
Types of stainless steel tanks in breweries
Mash Tun
The malt mashing tank is used to mix malt with water and convert the starch in the malt into sugar by heating and stirring. The tank is equipped with a heating system and a stirring device to ensure the smooth progress of the mash process.
Lauter Tun
The Lauter Tun is used to separate the wort obtained after mash from the malt residue. There are filter plates or mesh layers in the tank to help separate the wort and improve the efficiency of sugar extraction.
Boil Kettle
The boiling kettle is used to boil the wort and add hops for aroma and bitterness extraction. The heating system ensures that the wort reaches the boiling temperature, and the boiling time and the amount of hops added will affect the taste of the beer.
Fermentation Tank
The fermentation tank is where the yeast ferments and the yeast converts the sugar in the wort into alcohol and carbon dioxide. There are temperature control systems and pressure control devices in the tank to ensure the stable progress of the fermentation process.
Conditioning Tank
The maturation tank is used for further maturation and clarification of beer. It helps remove impurities and improves the taste and flavor of the beer, and some tanks can also be carbonated.
Bright Beer Tank
The Bright Beer Tank is where the beer is finally clarified and is used to store mature and clarified beer. It ensures that the beer maintains a consistent taste before packaging and allows for final carbonation adjustments.
Packaging Tank
The packaging tank is used to pack mature beer into bottles, cans, or kegs. It has a high-pressure gas injection system to ensure the carbonation level of the beer and complete the final packaging preparation.
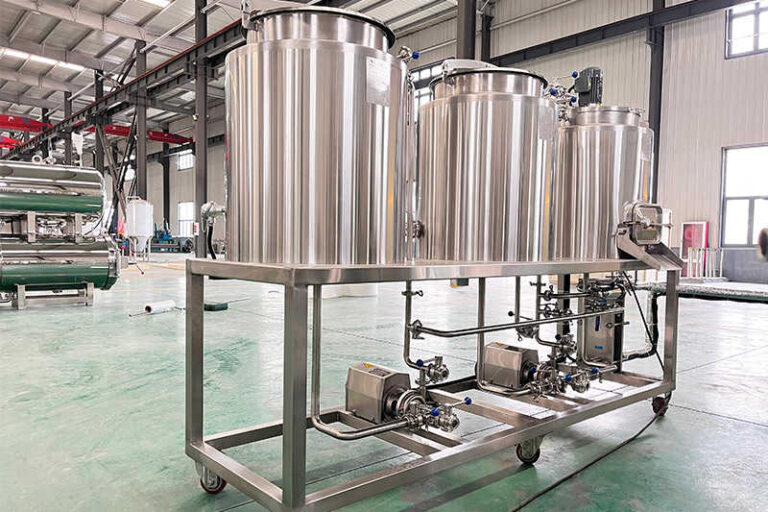
How to choose the right stainless steel brewing tank for your brewery?
Size and production requirements of breweries
When choosing a brewing tank, the first thing to consider is the production scale and target output of the brewery. Breweries of different sizes require different brewing tank capacities. Small craft breweries may only need smaller brewing tanks, while large-scale commercial breweries require larger capacities to improve production efficiency.
- Small craft breweries: If it is a craft brewery, the production volume is relatively small, and the tank capacity can range from a few hundred liters to a few thousand liters. Flexibility and process control are more important.
- Large-scale commercial breweries: Large-scale breweries require more efficient production equipment, and the capacity of brewing tanks is usually larger, reaching several thousand liters or even tens of thousands of liters. In this case, production efficiency, automation level, and durability are the selection keys.
Tank material and corrosion resistance
The material of stainless steel tanks is usually 304 stainless steel or 316 stainless steel, of which 304 stainless steel is more common. It has good corrosion resistance and easy cleaning and is suitable for most beer production. 316 stainless steel contains more molybdenum and has stronger corrosion resistance, especially suitable for some special environments, such as those that require acid or salt resistance.
Temperature control system requirements
Temperature control is a crucial factor in the brewing process. Different brewing stages (such as mash, fermentation, and maturation) require different temperature ranges, so the temperature control system of the brewing tank needs to be precise enough.
Cleaning and maintenance
Beer brewing is a highly hygienic process, so the cleaning and maintenance of the brewing tank are very important. The smoothness of the inner wall of the tank and the cleaning system (such as the automatic cleaning system CIP) directly affect the efficiency and thoroughness of cleaning.
Versatility and flexibility
Different types of beer (such as lager, ale, IPA, etc.) have different requirements for brewing equipment. For some craft breweries, it is crucial to choose a versatile and flexible brewing tank. Some brewing tanks are designed to perform multiple operations such as mash, fermentation, and maturation at the same time, which not only saves space but also improves production efficiency.
Budget
Although high-end stainless steel brewing tanks generally have better performance, they also mean a higher initial investment. Breweries should make reasonable choices based on their budgets, balancing equipment costs and savings in long-term use.
Supplier reputation and after-sales service
It is crucial to choose a reliable equipment supplier. The supplier’s reputation, equipment quality, and after-sales service (such as installation and commissioning, technical support, warranty period, etc.) all have a direct impact on the long-term operation of the brewery. High-quality after-sales service can help solve problems in equipment use and ensure that production is not disturbed.
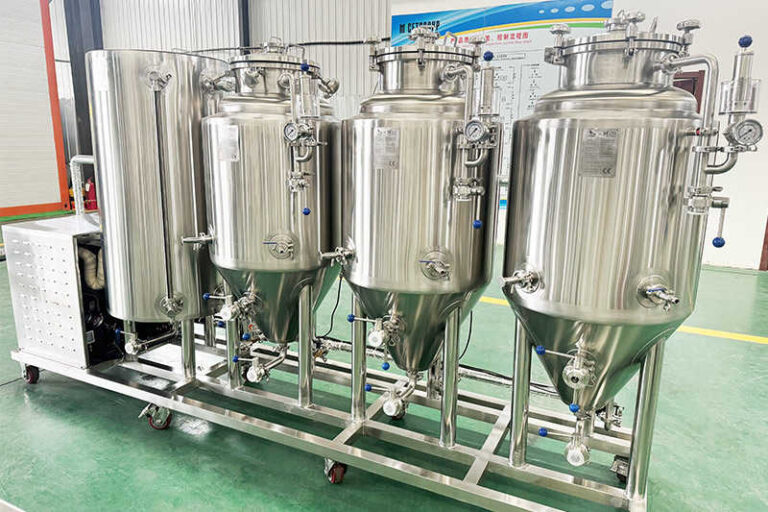
FAQ
What are the most common materials for brewery beer tanks?
Most brewery beer tanks are made of stainless steel because it is durable, corrosion-resistant, and easy to clean. Stainless steel is also inactive, ensuring that it will not affect the taste or quality of the beer.
How to determine the capacity of the brewing tank?
The capacity of the brewing tank should be selected based on the production scale of the brewery and the output of each batch of beer. Small craft breweries may need to reduce the size of the tank (such as 300L-1000L), while large commercial breweries usually choose larger tanks (such as 1000L-10000L).
Can I use these tanks for other beverages?
Yes, they are also suitable for the production of beverages such as wine, cider, and kombucha.
What size tank do I need?
This depends on your production scale and available space. Please consult the supplier for guidance.