What is a stainless steel tank?
A stainless steel tank is a storage container made of stainless steel material for storing liquids. It is widely used in chemical, food processing, medicine, environmental protection, water treatment, and other fields. In the brewing industry, it is used to store and process raw materials, fermentation liquid, or finished liquids such as beer, wine, and other fermented beverages. Stainless steel tanks can provide a closed and hygienic environment, which helps the stability and hygienic management of the brewing process.
Main features of stainless steel tanks:
- Large capacity: Storage tanks are usually designed as large-capacity containers that can store large amounts of materials, ranging from a few cubic meters to thousands of cubic meters.
- Corrosion resistance: Stainless steel materials have strong corrosion resistance to media such as acids, alkalis, salts, and moisture, and are suitable for storing various chemicals and corrosive liquids.
- Hygienic performance: Stainless steel has a smooth surface and is not easy to breed bacteria. It meets food-grade and pharmaceutical-grade hygiene requirements and is commonly used in the food, beverage, and pharmaceutical industries.
- Stable structure: Stainless steel storage tanks are usually designed as cylindrical or other stable structures, with high mechanical strength and high temperature resistance.
- Long life: Long service life, usually no frequent replacement or maintenance is required, and cost-effective.
- Environmental protection: Stainless steel is a recyclable material, and the storage tank itself is also more environmentally friendly.
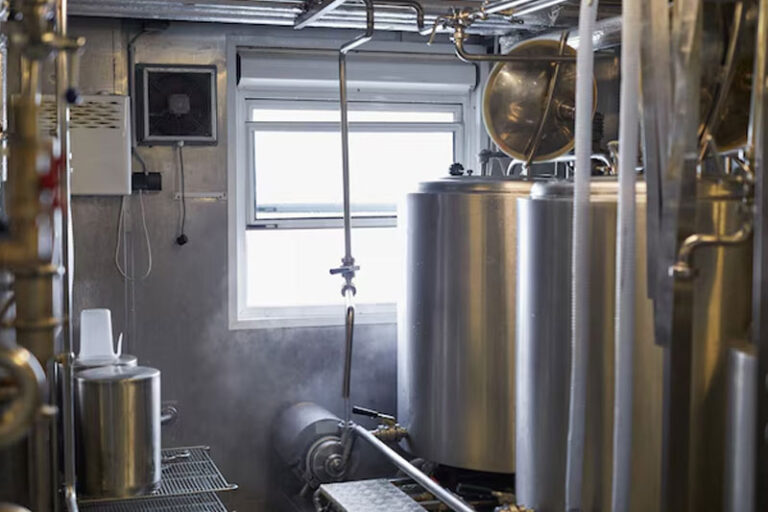
Comparison and analysis of stainless steel tank materials with other materials
Comparison with carbon steel tanks
- Corrosion resistance: Compared with stainless steel, carbon steel is prone to rust and corrosion, especially when it is wet or in contact with corrosive substances, and requires regular maintenance and anti-corrosion coating.
- Strength and durability: Although carbon steel has high strength, it has poor corrosion resistance and a short service life. It is easy to be corroded, resulting in a decrease in strength.
- Weight: Carbon steel generally has a higher density. Therefore, carbon steel tanks of the same volume are heavier than stainless steel tanks, which is not convenient for transportation and installation
- Cost: Carbon steel tanks have a lower initial cost, but poor corrosion resistance and oxidation resistance, resulting in increased maintenance costs.
Comparison with FRP tanks
- Corrosion resistance: Although FRP has good corrosion resistance, it is not as tolerant to certain special media such as strong acids and alkalis as stainless steel.
- Strength and durability: FRP has low strength and hardness. Although it can withstand a certain degree of pressure, it is easy to break under extreme conditions.
- Weight: FRP is lighter, easier to carry and install, and is especially suitable for lightweight tank design.
- Cost: FRP has a relatively low cost and is suitable for scenarios with limited budgets.
Comparison with aluminum alloy tanks
- Corrosion resistance: Aluminum alloy also has good corrosion resistance, but has poor tolerance to some specific corrosive environments.
- Strength and durability: Aluminum alloy has relatively low strength, limited load-bearing capacity, and is prone to deformation under heavy loads.
- Weight: Aluminum alloy is lighter and easier to transport and install, but has poor durability, which may shorten its service life.
- Cost: Aluminum alloy is relatively cheap and suitable for light-load, low-cost applications.
The impact of stainless steel tanks on beer quality
Maintain the purity of beer
- Prevent pollution: Stainless steel has excellent corrosion resistance and inertness, which can avoid releasing harmful substances when in contact with beer. Compared with materials such as carbon steel, stainless steel is less likely to react chemically with beer, thus maintaining the purity of beer.
- Smooth surface and easy to clean: The inner wall surface of the stainless steel tank is smooth, which reduces the attachment of microorganisms, is easy to clean and disinfect, and helps prevent pollution and maintain the taste and quality of beer.
Stabilize the flavor of beer
- Prevent oxidation: Stainless steel tanks perform well in sealing design and can isolate the entry of external oxygen, thereby avoiding flavor loss caused by oxidation.
- No odor migration: Stainless steel itself does not release odor or absorb ingredients in beer, so it can better maintain the original flavor of beer.
Improve the control of the fermentation process
- emperature control: Stainless steel has good thermal conductivity and is easy to install temperature control devices, so it can efficiently control the temperature of fermentation and storage, ensuring that the beer fermentation process is stable and the flavor is consistent.
- High-pressure resistance: Stainless steel tanks can withstand the pressure generated during the fermentation process and are suitable for fermentation or storage processes that require pressurization, thereby bringing a richer taste to the beer.
Extend the shelf life of beer
- Good sealing performance: The airtightness of stainless steel tanks can prevent the entry of air or other pollutants, thereby reducing the risk of beer contamination or oxidation and extending the shelf life.
- Corrosion resistance: Stainless steel tanks will not be corroded by acidic substances due to the long-term storage of beer, ensuring the service life of the tanks and the hygiene and safety of beer.
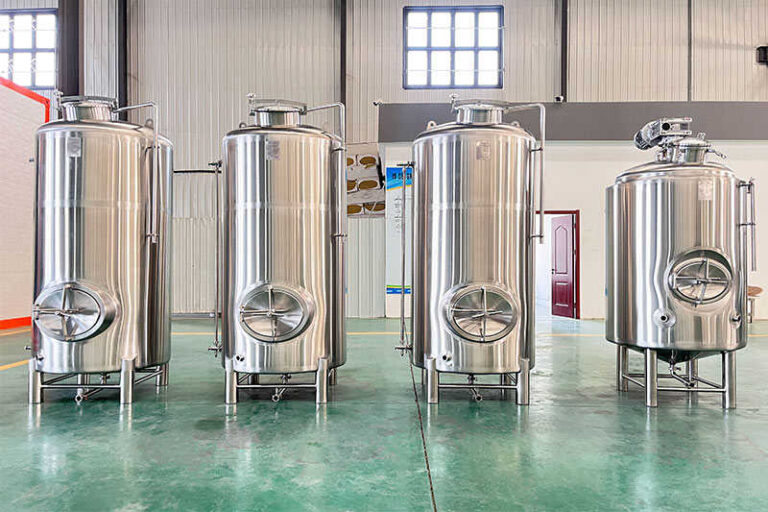
Influence on Beer Technology
- Suitable for various types of beer: The high adaptability of stainless steel tanks meets the fermentation and storage needs of various types of beer, from lager to ale.
- Customized design: Modern stainless steel tanks can usually be customized according to process requirements, including capacity, stirring device, temperature control system, etc., to help optimize the production process.
Price of stainless steel storage tanks
- Material type: Stainless steel storage tanks usually use materials such as 304, 316, and 316L. Among them, 304 is relatively cheap, while 316 and 316L are more expensive due to their higher corrosion resistance.
- Specifications and capacity: The capacity and size of the storage tank are important factors in determining the price. The larger the capacity, the higher the price.
- Design complexity: Whether the storage tank requires a special design, such as double-layer tanks (jacketed), mixing equipment, insulation layer, etc., will increase the cost.
- Manufacturing process and standards: Whether the manufacturing meets specific industry standards, as well as the requirements of welding, polishing, and other processes.
- Market supply and demand: Fluctuations in the price of stainless steel raw materials directly affect the cost of storage tanks, especially the price changes of nickel have a greater impact on 304 and 316 stainless steel.
Market prospects of storage tanks in the brewing industry
- The brewing industry is growing: The global demand for various alcoholic beverages is rising, especially beer, wine, and liquor. In particular, in markets such as Asia and Africa, alcohol consumption is growing rapidly. To meet market demand, breweries need to increase production capacity, and storage tanks are indispensable equipment in the production process.
- Storage tank technology is improving: Today’s storage tanks are becoming more and more high-tech. Not only are the materials more corrosion-resistant, such as stainless steel, lined with glass, etc., but many storage tanks have also added intelligent control systems that can monitor temperature, pressure, and liquid level in real-time to ensure the quality of the wine and higher production efficiency.
- Intelligence and automation: Breweries are increasingly introducing automated equipment, and storage tanks are no exception. Intelligent storage tank systems can automatically adjust and monitor various parameters, reduce manual intervention, improve production efficiency, and reduce waste. Therefore, the demand for this high-tech storage tank is also increasing.
- Environmental protection and sustainable development: Now everyone is paying attention to environmental protection, and breweries are no exception. Many factories will consider their environmental performance when choosing storage tanks. For example, some new storage tanks can reduce energy consumption and exhaust emissions, which is a great attraction for manufacturers, especially those breweries that focus on green production.
- Large-scale production: As the scale of wineries continues to expand, more large tanks have become a necessity, especially for those large-scale production plants. Large plants need more tanks to store raw materials and finished wines, which also drives the growth of market demand.
- Customized demand: Today’s wineries pay more and more attention to personalization and special flavors, so some plants will require customized tanks to meet specific production needs. This kind of customized demand provides more business opportunities for tank suppliers, especially for those who can provide special designs and technologies.

FAQ
What types of brewing are stainless steel tanks suitable for?
Stainless steel tanks are suitable for brewing beer, wine, whiskey, sake, and other fermented drinks. The material has good corrosion resistance and easy cleaning characteristics, suitable for various fermentation and storage needs.
Are tanks suitable for long-term storage of liquids?
Yes. Stainless steel tanks have good sealing and are suitable for long-term storage of liquids. But you need to pay attention to regularly check the seals and other interfaces to avoid leakage.
Does the inner wall of the tank need to be polished?
Yes. The inner wall of the tank usually needs to be mirror polished or passivated to reduce the adhesion of residues, reduce the risk of contamination, and ensure easy cleaning.
How to prevent oxidation problems in the tank?
- Ensure that the tank is well sealed to prevent outside air from entering;
- Use inert gas to protect the surface of the liquid;
- Clean regularly to avoid oxidation reactions caused by residues.