Have you ever heard brewers using different terms for their fermentation tanks? The brewing industry often uses various names that might confuse newcomers to the craft.
A fermentation tank is also commonly known as a fermenter, FV (Fermentation Vessel), or a unitank. These vessels are essential brewing equipment where wort transforms into beer through yeast fermentation.
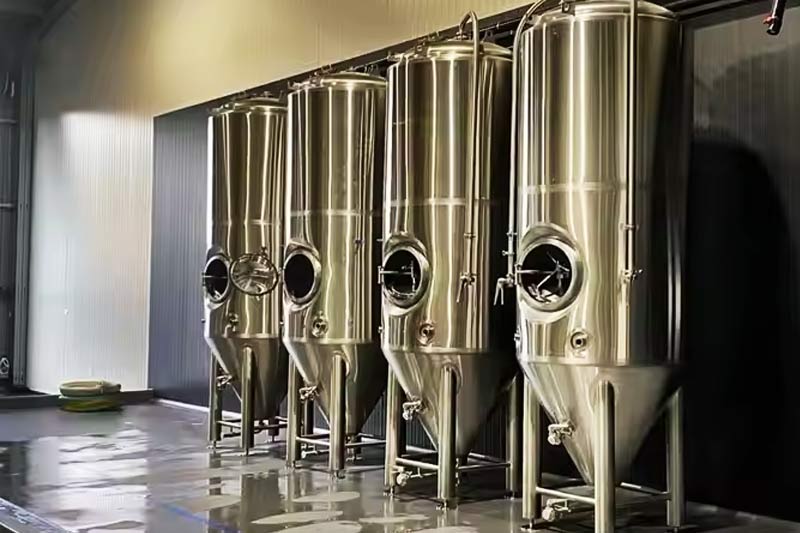
In my years of working with brewery equipment, I’ve noticed many brewers get confused about these terms. Let’s explore the different names and types of fermentation tanks to clear up any misconceptions.
Table of Contents
What is the Difference Between a Bioreactor and a Fermentation Tank?
When I first started in the brewing industry, I often confused these two terms. Many newcomers face the same challenge in understanding their distinct purposes.
While both vessels support biological processes, bioreactors are designed for various biological reactions, while fermentation tanks are specifically optimized for the fermentation of beverages like beer and wine.
Key Differences Between Bioreactors and Fermentation Tanks
-
- Purpose and Design
-
- Bioreactors:
-
- Used in pharmaceutical and biotechnology industries
-
- More complex control systems
-
- Multiple sensor ports for various parameters
-
- Higher sterility requirements
-
- Fermentation Tanks:
-
- Specifically designed for beverage production
-
- Simpler control systems
-
- Focus on temperature control and pressure regulation
-
- Food-grade materials and finishes
-
- Operating Conditions Feature Bioreactor Fermentation Tank Temperature Range -10°C to 80°C 0°C to 25°C Pressure Control High precision Basic regulation Agitation Multiple options Simple or none Monitoring Comprehensive Basic parameters
-
- Cost and Maintenance
The maintenance requirements and initial investment also differ significantly. A typical brewery fermentation tank costs between $10,000 to $50,000, while bioreactors can range from $50,000 to several hundred thousand dollars.
- Cost and Maintenance
Why Are Fermentation Tanks Conical?
I remember questioning this design choice when I first encountered conical fermenters. The answer lies in both efficiency and practicality.
Conical fermentation tanks feature a cone-shaped bottom that allows easy collection and removal of yeast and other sediment, improving beer clarity and simplifying the cleaning process.
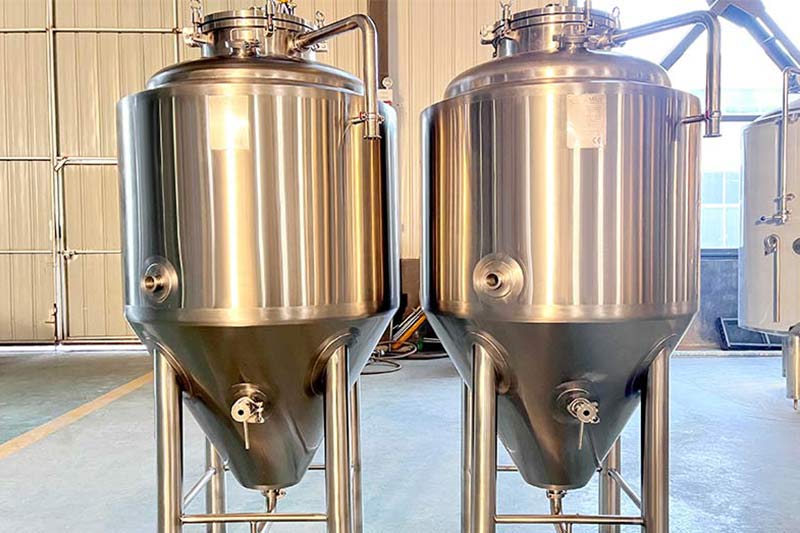
Benefits of Conical Design
-
- Yeast Management
-
- Natural yeast collection at the cone’s tip
-
- Easy harvesting through bottom valve
-
- Reduced beer loss during transfers
-
- Better control over fermentation process
-
- Cleaning Efficiency Feature Benefit Slope Angle Optimal 60° for sediment collection CIP Coverage Enhanced cleaning effectiveness Drain Design Complete liquid evacuation Access Points Easy maintenance access
-
- Space Utilization
The conical design also maximizes vertical space usage while maintaining efficient operation. This vertical orientation has become an industry standard, especially in craft breweries where floor space is premium.
- Space Utilization
Why Does Fermentation Tank Has Sealed?
In my experience supervising numerous brewing operations, proper sealing is crucial for successful fermentation.
Fermentation tanks must be sealed to maintain a controlled environment, prevent contamination, and capture CO2 produced during fermentation, ensuring consistent beer quality and safety.
Critical Aspects of Tank Sealing
-
- Pressure Control
-
- Maintains ideal fermentation conditions
-
- Prevents oxygen ingress
-
- Allows CO2 collection
-
- Controls fermentation rate
-
- Quality Assurance Factor Impact Contamination Prevention Ensures product safety Oxygen Exclusion Prevents oxidation Temperature Stability Consistent fermentation Aroma Retention Better flavor profile
-
- Safety Considerations
Proper sealing also addresses safety concerns, preventing pressure buildup while maintaining sanitary conditions. This is particularly important in larger operations where pressure management is critical.
- Safety Considerations
Are Conical Fermenters Better?
Throughout my career, I’ve worked with various fermenter designs, and this question comes up frequently from new brewery owners.
Conical fermenters offer superior functionality for professional brewing operations, providing better yeast management, easier cleaning, and more efficient space utilization compared to traditional cylindrical tanks.
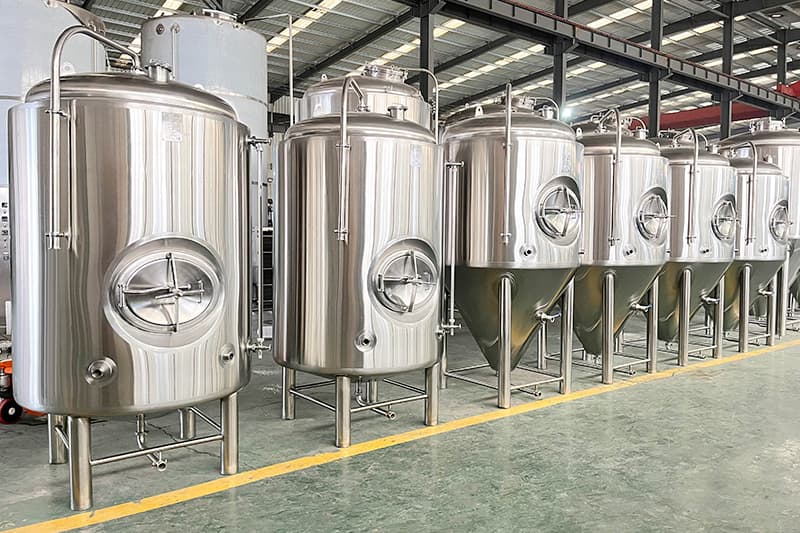
Comparing Fermenter Types
-
- Performance Analysis
-
- Yeast harvesting efficiency
-
- Product quality consistency
-
- Cleaning and maintenance requirements
-
- Space utilization
-
- Cost Comparison Feature Conical Cylindrical Initial Cost Higher Lower Maintenance Lower Higher Operation Efficiency Better Basic Long-term Value Higher Lower
-
- Practical Considerations
While conical fermenters require a higher initial investment, their operational benefits often justify the cost. The design reduces labor, improves product consistency, and provides better control over the fermentation process.
- Practical Considerations
Conclusion
From my extensive experience in the brewing industry, I can confidently say that understanding fermentation tank terminology and designs is crucial for successful brewing operations. The right choice depends on your specific needs and scale of operation.